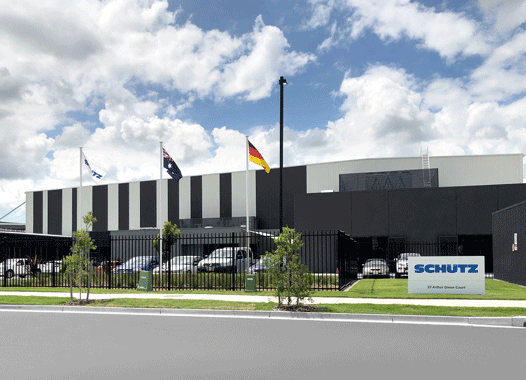
The new Schütz Australia factory was officially opened on the November 15 with a festive programme that also featured traditional elements of Aboriginal culture.
Around 100 guests, including numerous customers and suppliers, as well as representatives from the media, came to the opening in Yatala, south of Brisbane.
As well as ideal logistic connections, the new 19,000-square-metre company site has state-of-the-art facilities for the production of new IBCs, IBC and drum reconditioning, as well as high-performance storage and logistics facilities.
The new plant is an investment that will optimise supplies to customers in the eastern part of the country.
During a factory tour, guests watched the modern production lines operating live; all production facilities comply with the highest environmental, safety and quality management standards.
IBC reconditioning started here in January 2019; G2 110-litre drums used for agrochemical products are also returned to Yatala and reconditioned.
The next operational phase commenced in April, with the start of production of new containers on the Ecobulk MX line.
As the company’s new manufacturing hub on the east coast, the plant provides sustainable packaging and services to customers in Queensland and New South Wales.
It also significantly boosts delivery reliability and flexibility. In addition to the ultra-modern production facilities, the company’s local administration and sales offices are also located on the site.
Preserving tradition – shaping progress
The event began with an Aboriginal smoking ceremony. In accordance with the ancient customs of Native Australians, indigenous plants are smouldered to produce smoke that is believed to have cleansing powers and repel evil spirits.
After this traditional ceremony, Alan Barham, Managing Director Schütz Australia, Roland Strassburger, Schütz CEO, and Andreas Wolf, Business Unit Manager Asia/Pacific Schütz, welcomed the guests, who included Andrew Shields representing the Gold Coast Central Chamber of Commerce.
In his speech, Barham first thanked customers and business partners present for their many years of loyalty and excellent partnership.
He then summarised the 40-year history of the Australian Schütz subsidiary with its three locations in Melbourne, Perth and Yatala.
His speech concluded by highlighting the logistical, economic and ecological advantages of the new plant in Yatala.
In his speech, Wolf underscored Australia’s importance as a global supplier of raw materials and semi-finished products.
With its extensive range of packaging for liquid products, Schütz Australia makes a significant contribution to ensuring that a large proportion of these products can be shipped safely and quickly to customers in Australia and around the world.
He also stressed the aspect of sustainability – a key part of the company philosophy since the foundation of the Schütz Group and also a universal objective in Australia to ensure the protection of its unique flora and fauna.
As the biggest reconditioner of IBCs in the world, Schütz’s local activities not only include the collection of used IBCs and drums but also professional, resource-saving reconditioning in a closed-loop system.
Optimum logistics and recycling for effective sustainability
The new location is strategically located close to the major industrial regions of Brisbane and the City of Gold Coast.
The border between Queensland and New South Wales is about 50km away.
This location offers an ideal infrastructure with excellent access to national road and rail transport.
The port of Brisbane is only 40 minutes away for sea transport.
The new production plant will significantly optimise the supply chain to the many customers in the region – both economically and ecologically.
Shorter transport routes for the delivery of new IBCs and the collection of empty containers will save time, lower costs and reduce CO2 emissions.
The Schütz Ticket Service is also firmly established in Australia.
The empty Ecobulks are collected and reconditioned under the most advanced conditions and in compliance with globally uniform process standards.
All components that come into contact with the filling product, such as inner bottles, fittings and screw caps, are replaced with brand-new components.
The result is a Recobulk that corresponds fully in terms of safety and quality to an Ecobulk with the same standard specification and which, compared to a new IBC, saves around 100kg of CO2during production.