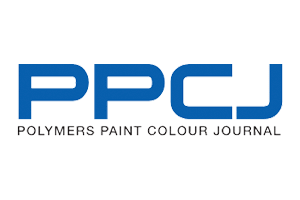
BASF has doubled its manufacturing capacity for UV acrylic hotmelts sold under the brand name acResin® by building a second production facility at the Ludwigshafen site in Germany.
By taking this step, the company has strengthened its position as the leading solution provider for sophisticated applications in the adhesives sector.
BASF invested several tens of millions of euros to build the new facility; the additional capacity it offers is now available.
"In the premium adhesives sector, the global trend is moving towards high-quality and sustainable application solutions. The UV-curable 100% acrylic hotmelt acResin meets these high requirements and, as a partner of the adhesives industry, we aim for continued growth in this specialty business,” explained Dr Jürgen Pfister, Vice President Business Management Adhesives & Fiber Bonding EMEA at BASF.
acResin is used to manufacture specialty products in the pressure sensitive adhesives sector.
These include labels for the food industry and various special adhesive tapes for the automotive and construction sector.
acResin offers both high-performance application properties and sustainability advantages.
In 2018, BASF carried out an eco-efficiency analysis of adhesive labels for durable goods: It found that, in comparison to solvent-based adhesives, acResin-based adhesives are both the less expensive and the more sustainable solution.
As a UV-curable 100% acrylic hotmelt, it contains only minimal amounts of volatile organic compounds (VOC) and is characterised by low levels of odour and good skin compatibility.
Other advantages offered by acResin are high transparency, outstanding resistance to ageing and heat, as well as resistance to water and chemicals.
In addition, acResin helps users of adhesives to fulfill the high requirements for food contact materials.