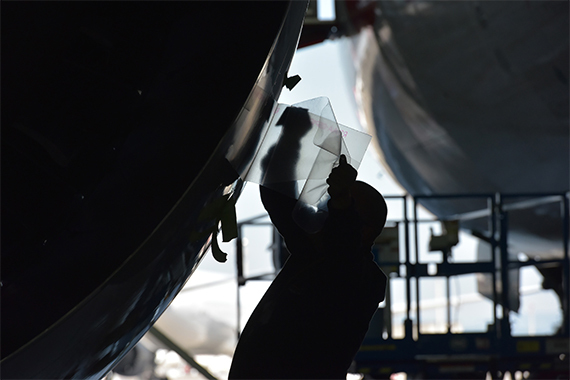
The European Union Aviation Safety Agency (EASA) has granted Lufthansa Technik a so-called Supplemental Type Certificate (STC) that officially paves the way for the series modification of two Boeing 777 variants with the fuel-saving AeroSHARK riblet films. Through the STC, the subfleet-wide roll-out of this sustainability technology, developed jointly by Lufthansa Technik and BASF, can now commence at the launch customers Lufthansa Cargo and Swiss International Air Lines (SWISS). The next modification layovers in Frankfurt and Zurich are already scheduled for early January.
Thanks to its special surface structure of microscopic ribs – so-called riblets – AeroSHARK reduces the frictional resistance of the aircraft skin. As a result, the fuel consumption and CO2 emissions are reduced by around one percent. For each Boeing 777-300ER operated by SWISS, this means annual savings of around 400 tons of kerosene and more than 1200 tons of carbon dioxide. The slightly shorter Boeing 777F saves around 370 tons of fuel and 1170 tons of CO2 each year.
A first AeroSHARK-equipped Boeing 777-300ER of the Swiss airline (HB-JNH), which also completed the flight test programme for the now-received certification, had already begun daily operations in October using a temporary "Permit-to-Fly” from the Swiss Federal Office of Civil Aviation (FOCA) that was valid for this single aircraft only. The STC issued by EASA now allows Lufthansa Technik to serially apply the nature-inspired riblet films to any given Boeing 777-300ER and 777F aircraft.
The AeroSHARK modification of HB-JNH already began at the end of August and culminated in so-called STC flights with EASA on September 8 and 9. During these flights, detailed proof had to be provided that the AeroSHARK modification had no negative impact on the operational safety and handling of the Boeing 777. The STC flight was followed by several weeks of evaluation of the collected data and other documents, such as measured values from flow simulations. After recently completing its review of all submitted documents, EASA finally granted the STC.
"The approval of AeroSHARK for the Boeing 777 variants is an important step in the distribution of this new technology for more sustainability in air transport,” said Soeren Stark, Chief Executive Officer of Lufthansa Technik. "With our partner BASF, we can now support our customers in making entire subfleets more climate-friendly. Moreover, we intend to realise the use of the new technology for further aircraft types. We are the only MRO company in the world to offer such solutions to reduce fuel consumption and CO2 emissions for commercial aircraft. We are naturally very proud of this.”
"Realising such a project is only possible through cooperation in partnership and great trust in each other’s expertise. Together, we have succeeded in developing a tailor-made solution that combines economic action and sustainability in equal measure,” explained Dr Uta Holzenkamp, head of BASF’s Coatings division and in this position also responsible for functional films. "With the Novaflex Sharkskin functional film, we are helping our customers to achieve their individual sustainability goals and in this way make aviation measurably more environmentally friendly.”
SWISS and Lufthansa Cargo will successively equip all 12 of their 777-300ERs and 11 777Fs with AeroSHARK. They will thus be the first passenger and cargo airlines worldwide to optimise a complete sub-fleet with the riblet films. Once all Boeing 777s at Lufthansa Cargo and SWISS have received their AeroSHARK modification, they will reduce the Lufthansa Group’s carbon footprint by more than 25,000 tons annually.
Lufthansa Technik and BASF intend to consistently develop AeroSHARK further for additional aircraft types and larger surfaces, so that in the future they can support airlines around the world in achieving their emissions targets. In initial model calculations, the sharkskin technology in its maximum expansion stage could even avoid CO2 emissions on the scale of up to three percent.