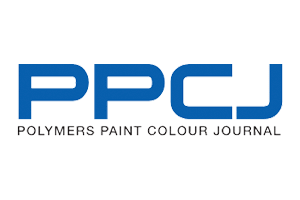
At interpack 2020, which is being held in Düsseldorf from May 7-13, BASF experts and specialists from BTC Europe, BASF’s European distribution organisation, will present a wide range of plastics, dispersions for adhesives, as well as resins and additives for printing inks and barrier coatings in hall 10, booth B43.
Solutions focus on the entire life cycle of the packaging products, from production and use to recovery options at the end of their service life.
They reduce the environmental footprint while remaining economically and socially viable.
Smart use of resources during production
In terms of production, the focus is on achieving process efficiency, product effectiveness and reduced emissions through the use of alternative feedstocks.
BASF is planning to showcase products made from bio-based raw materials obtained from responsible sources, as well as products made from recycled plastic waste.
The use of alternative feedstock helps conserve fossil fuels, reduces greenhouse gas emissions and diversifies the product range.
In addition, the mass balance approach ensures that more raw materials from organic waste and vegetable oils or plastic waste are used within BASF’s Verbund production system.
Alternative feedstock is added at the very beginning of the Verbund production system and then allocated to the respective sales products using an independently certified method.
The products are of the same quality and properties.
Another showcased solution to reduce emissions are BASF’s water-based technologies.
As an alternative to solvent-based technologies they improve occupational health and safety while reducing the CO2 footprint.
Added benefits during the use phase
During their use phase, packaging solutions have to ensure safe handling and reliably preserve the quality of the packaged goods.
BASF solutions provide added benefits such as lower packaging weight, which reduces the amount of resources used and packaging waste generated.
In addition, BASF materials maintain the safety and extended shelf life of packaged goods, an important factor for sensitive applications, such as the packaging of fresh foods.
At the same time, this helps to reduce food waste.
Tackling the end-of-life-challenges of packaging
At the end of its service life, the most appropriate recovery option should be chosen to manage packaging waste to keep it from being sent to landfills or incineration facilities.
BASF will be exhibiting solutions for the chemical, mechanical and organic recycling of packaging products.
BASF’s project ChemCycling™ focuses on chemical recycling to provide virgin-grade material based on recycled plastic waste, allowing the high-value recovery also for plastics for which there are currently no other recycling solutions or capacities are lacking.
In terms of mechanical recycling solutions, BASF has developed special adhesives for flexible packaging that facilitate the separation of multi-layer structures.
Furthermore, certified compostable materials make organic waste easier to collect and to recycle in large quantities.
This counteracts the inefficiency and the greenhouse gases emitted by other disposal ways for organic waste. At the same time, high-quality compost or organic feedstock is produced that can be used for new products.