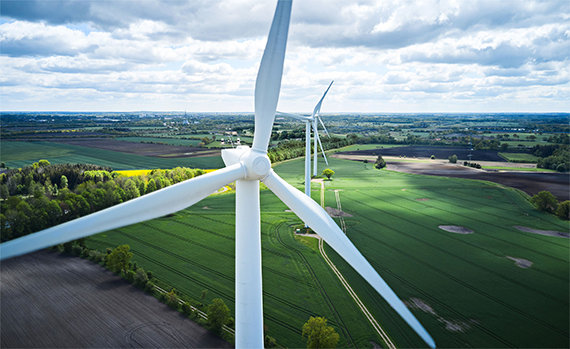
As a leading speciality chemicals manufacturer worldwide, BYK now has in its portfolio an additive with Germanischer Lloyd certification: BYK-C 8001. This means manufacturers of wind turbines can use the polymer coupling agent without further testing in their glass fibre reinforced epoxy resin systems – an important element in resource efficiency on the globally booming market for wind power.
As a rule, the rotor blades for wind turbines are manufactured using glass fibre reinforced plastic, a material for which BYK has been supplying products for decades. A single rotor blade often weighs more than four tons – and each wind turbine has three such rotor blades.
Given the limited space provided for wind power plants, the global trend is towards enhancing efficiency in existing plants or completely refurbishing entire wind parks. As a consequence of these developments, wind turbines are becoming larger and more effective. A concomitant aspect of this is longer and, especially, heavier rotor blades.
This is where the new BYK-C 8001 comes into play. The additive significantly enhances the mechanical strength of the material and, consequently, the robustness of the rotor blade, so that longer rotor blades can be manufactured at practically the same weight. Since the wind power market – just like the aviation market – only ever uses certified resources and raw materials, BYK decided to apply for BYK-C 8001 to be certified as the first additive worldwide, in spite of the minimal quantities of the additive actually used. This certification was undertaken by the globally recognised Germanischer Lloyd (DNV GL).
Up to 60% enhancements of mechanical properties and longer service life
BYK-C 8001 leads to substantial augmentation of the mechanical properties of rotor blades for wind power plants on account of the enhanced glass fibre matrix bonding. Special features include the design freedom and universal applicability, as the product is deployed in a liquid state, making dosage easy using amine hardeners, for example.
The BYK additive enhances the mechanical properties by up to 60%, since the coupling agent BYK-C 8001 is a copolymer with reactive/surface active groups that optimises the mechanical strength and the longevity of the fibre reinforced resins in the rotor blades. Results of fatigue tests directly indicate longer blade life. Another special feature is that it is deployable "irrespective of age” with every epoxy-compatible glass fibre fabric – while maintaining consistently high quality in the finished component.
Benefits for further applications
Needless to say, the additive is suitable for use not only in structural components, such as rotor blades for wind turbines, but also in comparable systems, such as automotive or aviation components. BYK-C 8001 is available worldwide. Using and/or adding the product in rotor blades for wind turbines is without consequences for existing certification.