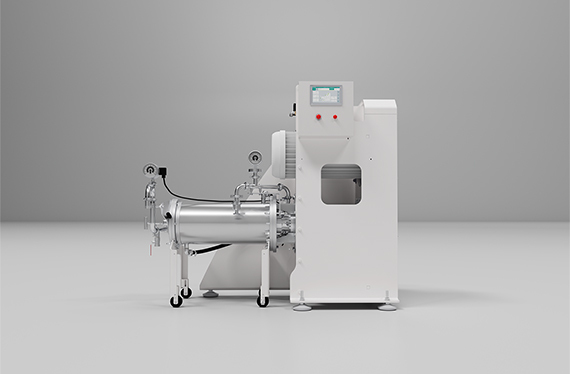
Bühler is taking its full-volume bead mill technology to the next level with the launch of Cenomic Optima. The newly reengineered version of Cenomic has a range of innovative technological improvements that result in higher flow rates, higher power inputs, and improved cooling to deliver up to 25% higher productivity. Now, the Cenomic Optima 3, with an active grinding chamber volume of around 20 litres, is available to customers globally.
Leading companies around the globe have been relying on Bühler’s Cenomic technology for many years, since the launch of the Centex in 2005 and its redesigned version, Cenomic, in 2013. With the freshly reengineered Cenomic Optima customers can use significant technological improvements to speed up their wet grinding operation while ensuring high quality output. "We constantly strive to innovate and substantially improve our solutions. It is part of our DNA. With Cenomic Optima, our customers will profit from a big increase in productivity,” says Angela Zürrer, Product Manager responsible for the Cenomic Optima at Bühler.
Cenomic’s technology is versatile. It has been used in a multitude of products, such as printing inks, automotive coatings, electronic pastes and many more. To fit every need, the Cenomic is available in diverse sizes, ranging from the Cenomic 1 with an active chamber volume of around 10 litres, the Cenomic 3 with 20 litres, to the Cenomic 30 with a volume of about 220 litres.
Cenomic’s novelties
ith Cenomic Optima, the customer will immediately experience measurable benefits:
- More efficient bead activation: The new solution has a clever configuration within the chamber that allows the Cenomic Optima to offer 37.5% more grinding disc surface for more efficient bead activation.
- Higher power input: The 30-kilowatt (kW) drive unit allows customers to increase the power input and thus reach the required specific energy for optimal grinding faster. This can improve productivity by up to 25% without increasing the footprint.
- Increased cooling capabilities: The ceramic inner liner ensures the products stay cooler during grinding. This allows the usage of the higher power input without breaching the product’s temperature limit.
- Higher flow rates: A larger screen diameter reduces pressure within the chamber and delivers at least 25% faster flow rates. This speeds up the process and avoids unwanted hydraulic packing.
Upgrade kit for customers
Two customers are already testing the Cenomic Optima and experiencing its indisputable benefits. The solution can be easily tested in Bühler’s Application Centres worldwide. For customers who already have a Cenomic, Bühler offers an upgrade kit, which will drive the productivity of the current mill by 25%.
Click here to learn more about Cenomic Optima and the coming upgrades of the other versions of this series.