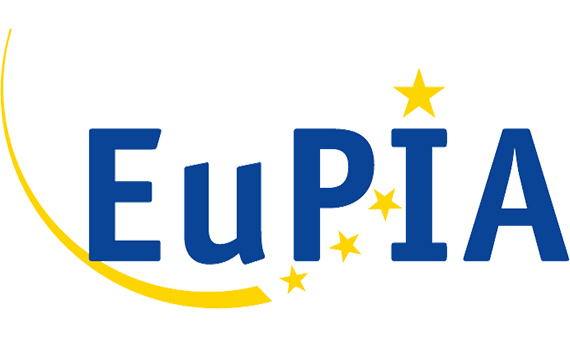
Across the industry, a number of compounding issues are leading to significant pressure on printing ink manufacturers across Europe. The increased cost of pigment raw materials, tightening upstream petrochemical supply chains, cost increases for vegetable oil derivatives and dramatically increased freight costs – due to the reduced availability of containers – are highlights of a myriad of destabilising factors.
In early 2021, the European Printing Ink Association (EuPIA) notes that manufacturers are already seeing an aggregation of factors, mostly triggered by the COVID-19 crisis, which are severely impacting the overall raw material supply chain. Whilst EuPIA members continue to work tenaciously to minimise risks to customers, they highlight the economic pressures impacting the printing inks market below.
Pigments Early in the first quarter of 2021, global pigment raw material costs (including Titanium Dioxide [TiO2]) have already seen sharp increases. Key drivers for the increases include: high demand across all industries, greater domestic supply requirements in producing countries, generic supply vs demand imbalances and higher pigment component costs. While the actual costs vary widely from region to region, higher than average per ton costs have been aggravated by significantly higher freight costs.
This early in the year, TiO2 supply is already restrained, with limited supply flexibility beyond regular volumes. This has resulted in significantly extended lead times to secure supply and further forecasting instability.
For coloured pigments, petrochemical feedstock cost increases, as well as increased logistics costs have coalesced to drive up finished pigment costs.
Petrochemicals In parallel to pigments, petrochemical raw materials (including UV resins, polyurethane resins, solvents and acrylic resins) have experienced higher costs. In Q2 2020, costs across the majority of petrochemical segments increased. Shortages of epoxy resins, high demand for polypropylene glycols utilised in the production of flexible foams and increases in acrylic acids have all been witnessed, dependant on location. In addition, due to ongoing freight constraints, manufacturers are experiencing longer delivery times and prolonged inflation of shipping container costs. All this volatility has led to additional complexity in logistical planning and difficulty in accurately predicting longer-term forecasts.
Vegetable Oils & Derivatives (Alkyd Resins/Esters)
From Q4 2020 and continuing into 2021, there has been an astounding vegetable oil price rally to six-year highs due to several developments compounding together. Palm oil production is at a three year low, while palm oil stocks worldwide are at low levels; soybean oil complex turned from a surplus to deficit with unfavourable weather conditions in the United States and drought damage in Latin America reducing both production & supplies – in addition Chinese imports & consumption has risen more sharply than expected. All these factors have impacted the cost of vegetable oils and their derivatives, such as alkyd resins and esters, which are the main backbone of paste ink used in both packaging and publication printing.
Freight The underlying issue affecting the majority of global commerce is a huge disruption in the world’s shipping trade. The catalyst for this disruption is the COVID-19 pandemic, which has triggered erratic demands for international trade. Previous shipping container movements (typically point-to-point and back again with some degree of regularity) have become more chaotic. As a result, containers have been sent to ports around the world where they have become stranded; many containers are now in the wrong parts of the world or in off-beat ports. The inequities between customer demand and short supply has resulted in a severe global shortage of freight capacity.
For perspective, prices of containers between China and Europe have risen more than 400% since Q4 2020.
Summary Raw materials and freight comprise the majority of the overall cost to produce printing inks. It is, therefore, inevitable that these higher material costs coupled to limited availability will have a major impact on the efficiency and resilience of producing companies. Exponentially higher freight costs will further exacerbate the current situation. As in the case of previous supply disruptions, EuPIA members seek to mitigate higher costs via internal process optimisation measures, alternate sourcing and increasing efficiencies.