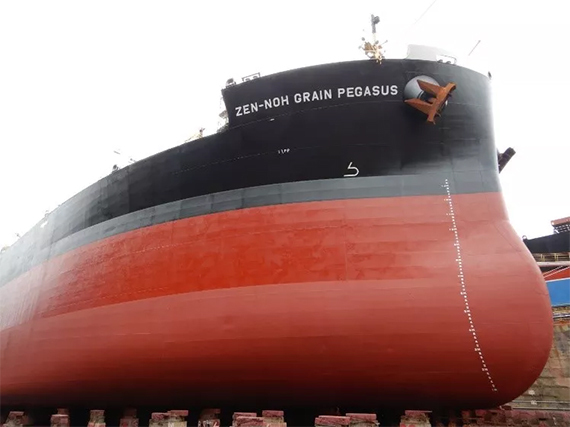
High freight rates and ongoing workforce limitations due to travel restrictions and COVID-19 measures are expected to result in Southeast Asia’s ship repair capacity falling by more than 25% compared to pre-pandemic levels, according to Nippon Paint Marine.
In 2019, a total of 516 vessels totalling 28mdwt drydocked at Singapore shipyards for paint jobs, but numbers dwindled to 296 ships in 2020 and 316 the following year as the world responded to the Covid-19 pandemic. Similar shortfalls are forecast at repair yards across Southeast Asia.
"We expect the number of vessels drydocking in the Asia Pacific region for a new coating to be 680-800, slightly up on the previous two years but still only 60-70% of the number of vessels that docked in 2019, which had a combined tonnage approaching 76 million deadweight,” said Bill Phua, Managing Director, Nippon Paint Marine (Singapore).
Having returned from recent visits to yards in Indonesia, Vietnam, Singapore and the Middle East, Phua noted that strict virus safety measures and travel restrictions in place to deal with the omicron variant are impacting the availability of workers to carry out the work.
"There’s still this limitation in place, restricting some yard’s achieving full capacity,” he said.
High freight rates are also expected to continue to affect repair volumes, as shipowners postpone scheduled drydockings to keep vessels trading.
"It does create planning problems, especially at Chinese repair yards where there are very strict quarantine protocols in place. Drydockings are taking considerably longer. We are seeing ships diverted to Vietnam, Dubai,” he said.
The increase in the number of vessels applying more fuel-efficient hull coatings, however, is expected to prove a boon for repair yards and coatings companies over coming months.
According to Phua, COP26’s Clydebank Declaration and the push to create "green shipping lanes” will result in a greater focus on hull coating technologies, given the environmental impact of biofouling, algae and barnacles on fuel consumption, especially when hulls are idle or slow steaming due to high port congestion.
"This is now a key consideration for operators specifying a hull coating. An idling ship is more attractive to marine life, so an antifouling that minimises this risk offers the operator a real and measurable commercial advantage,” said Phua.
Fouling results in speed loss, increased power demand, more fuel, increased costs and an increase in already high CO2 emissions. It also perpetuates the spread of invasive aquatic species to new environments, further affecting biodiversity and the marine ecosystem.
"The enforcement of ever stricter rules will require ship operators to comply and up the ante in terms of the technology adopted.
"Investing in greener coatings such as our new FASTAR® XI system can improve fuel efficiency by up to 8%, along with a 1.2% speed loss over a 60-month service interval. This helps shipowners better protect both the environment and their bottom line,” Phua said.
FASTAR’s reduced dry film thickness and fast drying time – up to 37% faster for a large container vessel, depending on the ambient local temperature – can also help vessel operators minimise time spent in drydock and keep vessels trading.
"This coating gives Nippon Paint Marine a clear commercial and environmental advantage over its competitors,” said Phua.